Global Technology Company’s Earthquake Experience Prompted a Search for a Solution
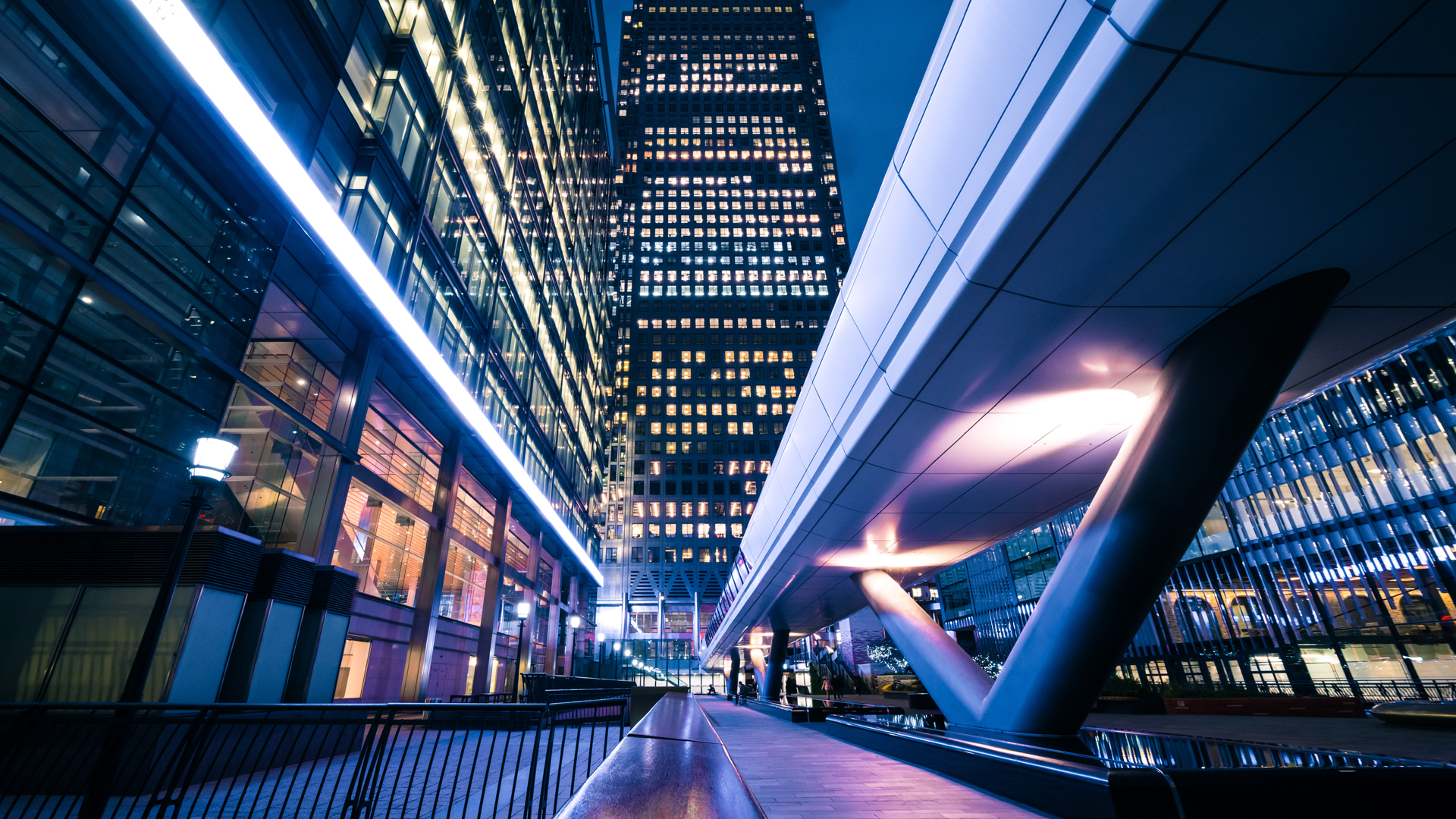
A major technology organization with offices and logistics centers across the globe, many in regions with high risk for earthquakes, sought a structural health monitoring solution that would help them be more proficient in responding to earthquake events and preventing unnecessary losses. Following a major event at its location in Mexico City, the company’s crisis management team began a year-long initiative that resulted in a partnership with Safehub.
Earthquake Event in Mexico City Triggers a Major Initiative
On September 19, 2017, a 7.1-magnitude earthquake event jolted Mexico City with continuous strong shaking for approximately 20 seconds. The earthquake impacted a large area, causing more than 200 fatalities and many more injuries, as well as extensive damage and destruction to hundreds of buildings.
Erring on the side of caution, the business continuity and crisis management team at the local offices of a large global technology company made the decision to deem the company’s two buildings located in the quake area as unoccupiable. Although there was no visible physical damage, they could not be certain about whether there was structural damage. As a result, operations were shut down and 2,400 employees were evacuated until any potential structural damage to the buildings could be determined.
Around the same time, awareness of the probability of damages from future potential earthquakes was growing at the company’s global headquarters, which was located near a major fault on the West Coast. An article in the Seattle Times that warned of the potential catastrophic damage of a 9.0 megaquake had heightened awareness and concern among executive leadership—and the Mexico City event brought a new focus on the urgent importance of structural health monitoring in preparedness and responsiveness.
A Shutdown Leads to a Solution
The immediate issue at hand was determining the amount of structural damage, if any, that had been sustained by the buildings in Mexico City. With all the damage that had occurred in the area, the company was unable to contract a local structural engineer on a timely basis. Instead, after two weeks of delay, they were able to contract engineers from a U.S.-based engineering team, who then determined that the buildings had likely not sustained structural damage.
As a result of the two-week shutdown, the company incurred considerable business interruption costs. Because nearly all (about 90 percent) of the local workforce was not able to work remotely, operations were suspended for the entire two-week period.
Armed with a high level of awareness and interest in finding a catastrophe risk management and structural health monitoring solution, the company attempted to craft its own solution. This included connecting software developers with a seismic engineering firm to develop a solution. The goal was to create a solution that would ensure the safety of the company’s personnel, prevent downtime, and minimize costs. After several developmental challenges, the company was introduced to Andy Thompson, Safehub’s CEO and the Safehub team.
A Gradual Global Deployment
Deployment of Safehub’s structural health monitoring solution began, starting with a rollout at 35 of the most critical buildings, where the brain trust of the company was headquartered, then on to all the company’s buildings in the surrounding area.
Over a period of two years, the deployment of building sensors went global, with a priority on installations in countries that posed the highest earthquake risk –beginning in Japan and on to Indonesia, Costa Rica, and the Philippines.
Because Safehub shipped the building sensors to each location, deployment of the solution was quick and easy. Each on-site installation team installed the compact wall plate with two screws onto the wall and plugged them in.
“Anyone who can hang a picture can do this. The fact that the sensors are connected to cellular and don’t need to be connected to a network adds to the convenience and installation simplicity. It’s also a big plus that we only need two sensors—on the top and bottom floors.”
Global Technology Company’s Representative
The technology company finds great value in Safehub’s automated messaging feature, which immediately alerts key decision-makers when an event occurs and provides an account of the event with valuable, actionable data customized to the actual facility. After the local crisis management team—and a structural engineer, when necessary—inspect the structural health monitoring data, they are now also armed with valuable granular data from Safehub’s platform on which to base their determinations.
“We used Safehub to conduct an immediate assessment and its results were verified by employees on the ground…no known damage.”
Crisis Manager at Global Technology Company
The Undocumentable Value of Safety
The two weeks of unnecessary downtime in Mexico City is just one demonstration of the need for a crisis responsiveness solution like Safehub.
“We now understand the importance of a solution like Safehub, which provides us with concrete data to make informed decisions about business continuity that will prevent serious losses of productivity and revenue.”
Global Technology Company’s Representative
More important than revenue losses, however, is improving the safety of the company’s personnel—an invaluable benefit to having real-time, building-specific data. Having a scalable structural health monitoring solution like Safehub now allows this technology company to significantly increase employee safety, without drastic financial implications.
“We place great emphasis on the safety of personnel, so there are benefits beyond any financial savings — and those financial savings alone likely more than pay for the costs of the system.”
Global Technology Company’s Representative
Get Started Today
Request a demo to learn how we can help minimize your risk during disasters with building-specific, real-time data.